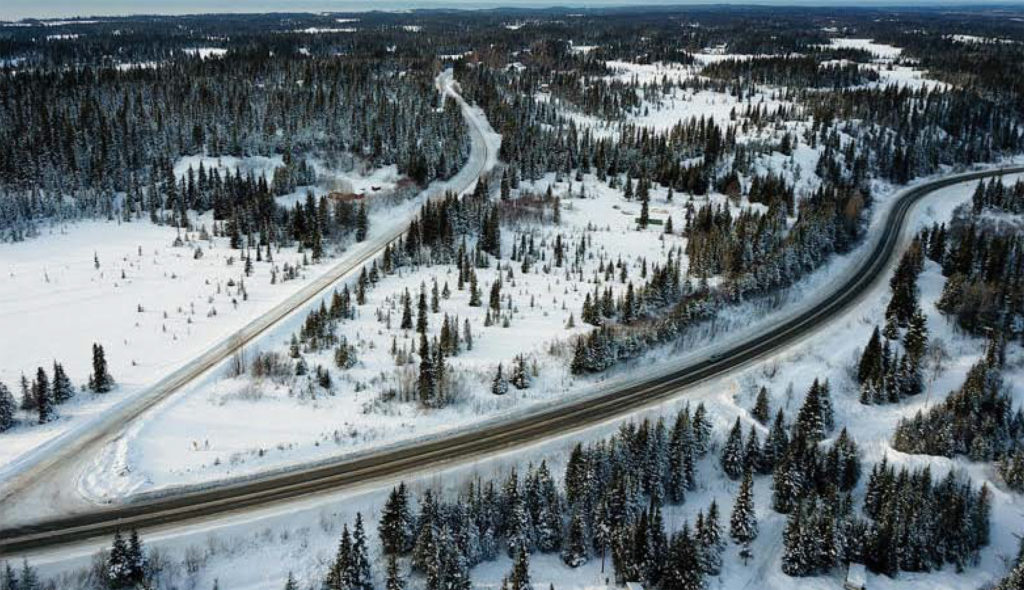
Student Members
- Michele Lott
- John Scott
- Jayci VanDehey
Client
- EIT Imagineering Inc.
Partners
- Scott Hamel, Ph.D, PE, SE-Daniel King, PE
- Steven Halcomb, PE, GE, D.GE, ENV SP
- Josh Bablonka. HMS
- Paul Taylor
Overview
Paul Taylor, a private client from Homer, Alaska, has always dreamed of living in a tree house. His desire is to live above the trees with a complete 360-degree view. Taking the first step to achieve this goal, he has asked Imagineering Inc. to help him start the design of his dream home.
Imagineering Inc. completed a feasibility study for Paul Taylor’s dream home. This included three design alternatives for the superstructure and 2 design alternatives for the foundation design. All design elements were taken to a 10% completion design to help the client determine his preferred design alternative.

Design Alternative A consisted of a special concentrically braced frame. It used steel HSS members for the columns and braces, and W-sections for the beams. The steel weight of the structure was 92,000 lbs. Because it is a special concentrically braced frame, it has a response modification factor of 6 for seismic loads, which is important for calculating the structure’s response to earthquakes. However, it was determined that wind forces governed the design of the structure.

Design Alternative B consisted of eccentrically braced frames. It used steel HSS members for the columns and braces, and a W-section for the beams. The steel had a weight of 91,000 lbs and because its eccentrically braced, the structure has a response modification factor of 8 for seismic loads which is way this alternative was chosen as an option; however, wind forces also governed the design of this structure. If the structure had been governed by seismic loads, the quantity of steel could have been reduced.

Design Alternative C consisted of 64 ft of timber shear walls and a 16 ft concrete podium at the base of the structure. It is a fully enclosed structure. For the construction, 2×10 studs at 24 in. on center were assumed. The plywood was determined to require double sheathing, on the exterior and interior of the studs. The governing load on the structure was wind. The uplift between the timber walls and the concrete podium was very large, which may be difficult to counteract with connections.
Recommendation
We recommend Design Alternative A. Despite this structure not having the lowest cost of the three design alternatives, its cost can be reduced with further engineering. Each level of the tower can be further optimized to decrease cost. With Design Alternative A, we recommend using the driven piles, as they are more appropriate for unknown soil conditions with large loads and a high-water table.
Foundation Alternatives
Shallow Foundation

For the shallow foundation, excavation would be required. The depth of the excavation required factors like the water table, soil composition. And the frost depth to be considered. The foundation was designed to resist the overturning of the structure and it was determined there would be 4 concrete pads, one at each tower leg. The pad would be 9 ft x 9 ft and placed 6 ft deep. This design is adequate for Design Alternatives A and B.
Pile Foundation

For the driven pile foundation, the assumptions were made that there is a 5-foot deep active frost layer on the property. The design determined there would be one steel pile at each tower leg. Based on the overturning forces on the tower from wind and seismic, the design determined that the piles needed to be 50 feet in length with 24” diameters. This design was determined to work for Design Alternatives A and B. Design C would require 3 piles at each leg.
Cost Estimates
Tower Design Alternative | Basic Cost Estimate |
---|---|
Design A | $453,000 |
Design B | $448,000 |
Design C | $183,000 |
Foundation Alternatives | Basic Cost Estimate |
---|---|
Shallow | $52,000 |
Pile | $86,000 |
For the cost estimates of the three alternatives, we reached out to a professional cost estimator from HMS, Inc. The cost estimates were the total project cost, including contractor mark ups, insurance, renting equipment, fuel, etc. It also captured the costs of the geographic location- Homer, Alaska- by looking at what contractors are bidding for projects in that region. The pile foundation cost estimate also included a subtractor’s markup, since it is unlikely a contractor will have pile driving rigs.
Recommendation
We recommend Design Alternative A. Despite this structure not having the lowest cost of the three design alternatives, its cost can be reduced with further engineering. Each level of the tower can be further optimized to decrease cost. With Design Alternative A, we recommend using the driven piles, as they are more appropriate for unknown soil conditions with large loads and a high-water table.

Comments are closed